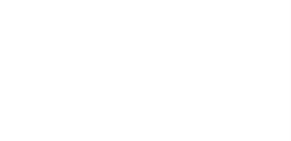
The phrase “too good to be true” often suggests skepticism, especially when discussing advanced technology like handheld laser welder machine. Many people in the metal fabrication and manufacturing industry may wonder whether this device is truly as effective, versatile, and efficient as manufacturers claim. While handheld laser welding machines have gained immense popularity in recent years, certain doubts and misconceptions surround them.
To understand whether these concerns are valid, let’s break down the possible reasons why a handheld laser welder might seem too good to be true and analyze whether these concerns hold any merit.
1. Portability vs. Power β Can a Compact Welder Deliver Strong Welds?
Traditional welding methods, such as TIG (Tungsten Inert Gas) and MIG (Metal Inert Gas) welding, typically require large and stationary setups. The idea that a small, handheld laser welder can produce high-quality welds without the need for heavy machinery may sound unrealistic.
Reality Check:
Handheld laser welding technology utilizes concentrated energy from a laser beam to fuse metals. Unlike traditional methods that rely on electrode or filler materials, laser welding offers deep penetration and high-strength welds without excessive heat distortion. Advanced fiber laser technology ensures that a compact machine can deliver sufficient power (ranging from 1000W to over 3000W), making it highly effective for a variety of applications.
2. Speed vs. Precision β Can a Handheld Device Maintain Accuracy?
Many users believe that welding requires steady hands and precise control. The thought of using a handheld laser welder for intricate welding work raises concerns about accuracy and consistency.
Reality Check:
Handheld laser welders are equipped with an adjustable laser beam that can be fine-tuned based on the thickness and type of metal being welded. Additionally, the use of an automated wire feeder and pre-set parameters reduces human error. With minimal training, operators can achieve highly precise and clean welds, even on complex joints.
3. Heat and Safety β Is It Truly a βCoolerβ Alternative to Traditional Welding?
One of the most common concerns is the heat generated during welding. Traditional welding produces extreme heat, sparks, and smoke, raising questions about whether a laser welder can operate safely without causing burns, warping, or material damage.
Reality Check:
Laser welding is known for its low heat input compared to traditional welding. The laser beam focuses on a small, controlled area, significantly reducing heat dispersion. This means less warping, minimal burn-through, and a safer work environment. While safety precautions like protective eyewear and proper ventilation are necessary, laser welding produces far fewer hazardous fumes and sparks.
4. Versatility vs. Limitations β Can It Weld All Metals and Materials?
Some fabricators wonder whether a handheld laser welder can handle all types of metal, including aluminum, stainless steel, copper, and titanium.
Reality Check:
Handheld laser welding machines are highly versatile and can weld a wide range of metals, including reflective materials that are challenging for traditional welding techniques. However, they do have some limitations, such as difficulties welding thick cast iron or extremely thick steel sections beyond a certain depth. Understanding material compatibility is essential to maximizing efficiency.
5. Cost vs. Long-Term Value β Is It Worth the Investment?
Many manufacturers hesitate to adopt laser welding due to the initial cost of the machine, which is significantly higher than traditional welding equipment. This raises the question: Is a handheld laser welder truly cost-effective in the long run?
Reality Check:
While the upfront cost of a handheld laser welder is higher, it provides significant long-term savings. The faster welding speed, lower maintenance costs, minimal consumables, and reduced post-weld finishing requirements make it a cost-effective choice over time. Additionally, labor efficiency increases since operators can complete tasks more quickly and with higher precision.
6. Ease of Use vs. Training Requirements β Is It Truly βPlug and Playβ?
Some people think that advanced welding technology requires extensive training to operate effectively. The idea that a handheld laser welder is user-friendly sounds too good to be true.
Reality Check:
Handheld laser welders are designed for simplicity and ease of use. Unlike traditional welding, which requires years of practice to master, laser welding allows new operators to become proficient within days. The interface includes automated settings, adjustable parameters, and ergonomic designs, making the transition from conventional welding much easier.
7. Maintenance vs. Downtime β How Reliable is a Handheld Laser Welder?
A common concern is whether a high-tech laser welding machine is prone to frequent breakdowns or high maintenance costs.
Reality Check:
Laser welding machines require significantly less maintenance than traditional arc welding machines. With fewer moving parts, no electrode replacements, and minimal consumables, the likelihood of breakdowns is lower. Regular cleaning of the optics and proper cooling system maintenance can keep the machine running smoothly for years.
Leave a Reply