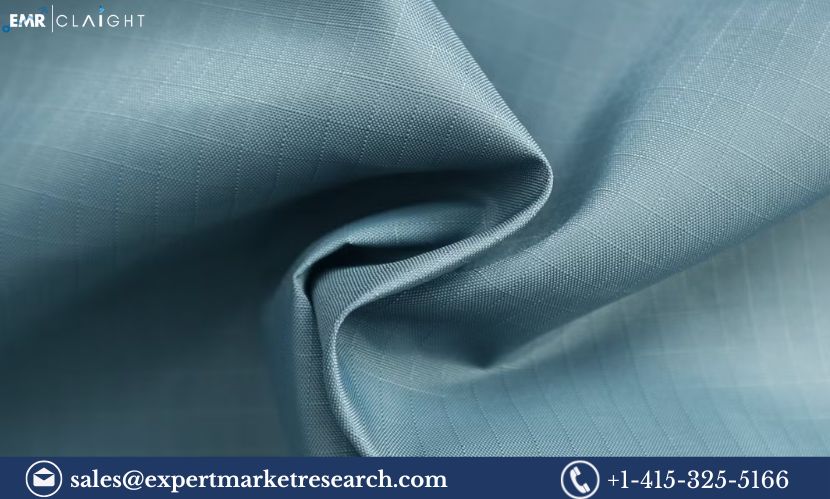
Introduction
Nylon, a synthetic polymer fabric, has become an essential material in various industries, including textiles, automotive, and manufacturing. Known for its durability, elasticity, and resistance to abrasion, nylon fabric has widespread applications in clothing, industrial fabrics, and consumer goods. As one of the most versatile synthetic fibers, nylon has continued to maintain strong demand in both consumer and industrial markets. With the increasing growth of the fashion and automotive industries, there is a rising need for high-quality nylon fabrics. This makes the establishment of a nylon fabric manufacturing plant an attractive business opportunity for entrepreneurs and manufacturers. A Nylon fabric manufacturing plant project report serves as a detailed guide for setting up a plant that produces nylon fabric efficiently and meets market demands. The report covers important aspects of the business, such as the raw materials required, production processes, key equipment, market potential, and financial projections, providing a clear roadmap for potential investors and entrepreneurs in the fabric manufacturing industry.
Market Overview and Growth Prospects
The global market for nylon fabric has been experiencing steady growth over the years. The textile industry, particularly the fashion and apparel segments, is one of the largest consumers of nylon fabric. The growing demand for lightweight, durable, and versatile fabrics in various applications is driving the expansion of the nylon fabric market. Additionally, the automotive, aerospace, and industrial sectors also contribute significantly to the demand for high-performance nylon fabrics, which are used in components such as seat belts, airbags, and industrial ropes.
Key drivers of the nylon fabric market include:
- Rising Demand for Sportswear and Activewear: The growing popularity of activewear and sportswear, which often incorporates nylon fabrics due to their lightweight and stretchability, has positively impacted the nylon fabric market.
- Increased Demand for Durable and Lightweight Materials: Nylon’s high strength-to-weight ratio makes it a preferred material for a variety of applications, including outdoor gear, luggage, and upholstery.
- Technological Advancements: Advances in fiber technology have led to the development of high-performance nylon fabrics that offer enhanced properties, such as water resistance, anti-bacterial features, and UV protection.
- Environmental Considerations: As sustainability becomes a priority in the textile industry, the use of recycled nylon (such as nylon made from post-consumer waste or ocean plastics) is gaining momentum, presenting new market opportunities for manufacturers.
The growth of these key sectors ensures a stable and promising future for nylon fabric manufacturing, with demand continuing to rise in both established and emerging markets.
Get a Free Sample Report with Table of Contents@
Key Components of a Nylon Fabric Manufacturing Plant
Establishing a nylon fabric manufacturing plant requires significant planning and investment in infrastructure, equipment, and raw materials. Below are the key components involved in setting up such a facility.
1. Raw Materials and Ingredients
The production of nylon fabric begins with the preparation of the raw materials, which are essential for creating the synthetic fibers. The primary raw materials involved in nylon fabric production are:
- Nylon Resin: The key raw material for manufacturing nylon fabric is nylon resin, usually produced through a polymerization process. The most common types of nylon used in fabric production are Nylon 6 and Nylon 6,6, which differ in their polymer structure and properties.
- Additives: Additives such as dyes, flame retardants, and plasticizers may be used to enhance the fabric’s properties, such as color, texture, and resistance to wear and tear.
- Recycled Nylon: With a growing focus on sustainability, many manufacturers are opting to use recycled nylon, which can be sourced from post-consumer products, waste fabrics, or discarded nylon products like fishing nets or plastic bottles.
The quality of the raw materials used in the production process directly affects the quality of the final fabric. Therefore, ensuring a reliable supply of high-quality nylon resin is crucial for the success of the manufacturing plant.
2. Manufacturing Process
The production of nylon fabric involves several key steps, which convert the raw materials (nylon resin) into fabric. The manufacturing process includes the following stages:
Polymerization
The first step in the nylon fabric manufacturing process is polymerization, where the nylon resin is synthesized from chemicals like hexamethylenediamine and adipic acid (for Nylon 6,6) or caprolactam (for Nylon 6). During polymerization, these chemicals undergo a reaction to form long chains of molecules that make up the nylon polymer.
Extrusion and Spinning
Once the nylon polymer is prepared, it is heated and melted, then passed through spinnerets to form fibers. The process of extruding the nylon polymer through these small holes creates filaments that are cooled and solidified into fibers.
The type of extrusion and spinning process used depends on the desired characteristics of the fabric. For example, filament yarns are used for smoother, finer fabrics, while staple fibers may be used for thicker, more textured fabrics.
Drawing and Stretching
After the nylon fibers are spun, they are drawn (stretched) to align the polymer molecules, which increases the strength and elasticity of the fabric. The drawing process may involve passing the fibers through a series of rollers to stretch them to the desired thickness and strength.
Texturing and Weaving
Once the nylon fibers are drawn, they may be texturized to give them a particular texture or appearance. Texturizing can be done using processes like false twist or air-jet texturing, which create crimps and twists in the fibers, enhancing their elasticity.
Next, the nylon fibers are woven or knitted into fabric using traditional weaving looms or modern knitting machines. The weaving process involves interlacing the fibers in a specific pattern to create fabric, while knitting involves looping the fibers to create a flexible, stretchable material.
Finishing
The finishing process is crucial for enhancing the fabric’s properties. This may involve processes such as dyeing, printing, coating, and adding additional treatments like water resistance, flame retardancy, or UV protection. Finishing also helps improve the fabricβs aesthetic qualities, such as color and texture.
Quality Control
Throughout the manufacturing process, strict quality control measures are implemented to ensure that the nylon fabric meets the required standards for strength, durability, color fastness, and other properties. Testing is done at various stages, from raw materials to the final fabric, to verify that the fabric is of high quality and free from defects.
3. Manufacturing Equipment
A nylon fabric manufacturing plant requires several types of specialized equipment to ensure efficient production. Key equipment includes:
- Polymerization Reactors: Used for synthesizing nylon resin from the raw chemicals.
- Extruders: Used for melting and extruding the nylon polymer into fibers.
- Spinning Machines: Machines that spin the polymer into filaments or fibers.
- Texturizing Machines: Equipment used for creating textured yarns or fabrics.
- Weaving or Knitting Machines: Looms and knitting machines that interlace or loop fibers into fabric.
- Dyeing and Finishing Machines: Equipment for dyeing the fabric and applying finishing treatments such as water resistance or UV protection.
- Quality Control Instruments: Machines and tools for testing fabric quality, such as strength testing machines, color spectrophotometers, and moisture analyzers.
4. Plant Layout and Design
Designing an efficient nylon fabric manufacturing plant involves creating a layout that facilitates smooth production flow, minimizes waste, and ensures worker safety. Key considerations for plant layout include:
- Raw Material Storage: A designated area for storing nylon resin and other raw materials, ensuring proper handling and easy access.
- Production Zones: The plant should have clearly defined zones for polymerization, extrusion, spinning, weaving or knitting, and finishing processes, with minimal movement of materials between stages.
- Quality Control Areas: Dedicated spaces for testing raw materials and finished products, ensuring that all fabric produced meets required standards.
- Safety and Environmental Controls: The facility should be equipped with fire suppression systems, ventilation, and waste management systems to ensure worker safety and compliance with environmental regulations.
5. Regulatory Requirements and Compliance
Nylon fabric manufacturing plants must comply with various industry regulations and standards, including:
- Environmental Regulations: The plant must adhere to environmental laws regarding waste disposal, emissions, and chemical usage, ensuring that the production process is sustainable and does not harm the environment.
- Occupational Health and Safety Standards: The plant must comply with workplace safety regulations to protect workers from hazards such as chemical exposure, machinery accidents, and respiratory risks.
- Textile Standards: The fabric must meet specific standards for strength, durability, color fastness, and other performance characteristics, depending on the intended application.
6. Financial Projections and Investment Considerations
The financial feasibility of a nylon fabric manufacturing plant depends on several factors, including capital investment, production capacity, operating costs, and revenue potential. Key financial considerations include:
- Initial Investment: The cost of setting up the plant, purchasing machinery, and acquiring raw materials.
- Operating Costs: Ongoing expenses, including labor, energy, raw materials, maintenance, and packaging.
- Revenue Generation: Projected revenue based on market demand for nylon fabrics, pricing strategies, and production capacity.
- Return on Investment (ROI): Detailed financial projections should be prepared to estimate ROI, payback period, and profitability.
Media Contact
Company Name: Claight Corporation
Contact Person: Lewis Fernandas, Corporate Sales Specialist β U.S.A.
Email: sales@expertmarketresearch.com
Toll Free Number: +1β415β325β5166 | +44β702β402β5790
Address: 30 North Gould Street, Sheridan, WY 82801, USA
Website: www.expertmarketresearch.com
Aus Site: https://www.expertmarketresearch.com.au
Leave a Reply