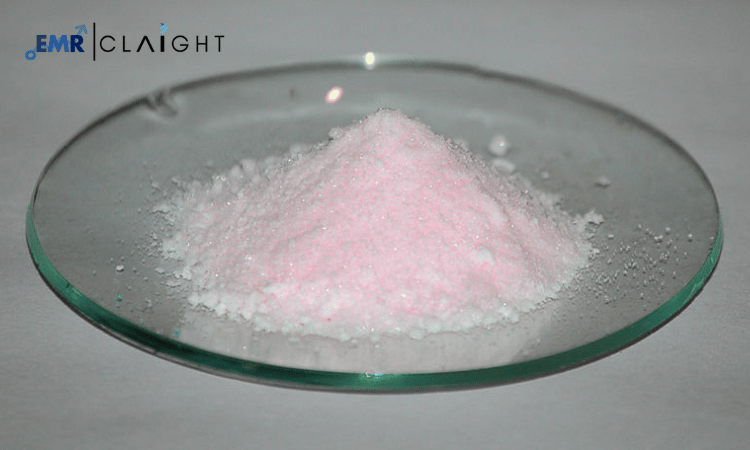
Manganese(II) sulphate, a compound commonly used in various industrial applications, has gained significant importance in recent years, especially in the field of battery production and agriculture. As an essential raw material, it is utilized in the manufacture of lithium-ion batteries, animal feed, fertilizers, and in several other industries. The growing demand for electric vehicles (EVs), coupled with the rise in global interest in sustainable energy sources, has led to an increased need for manganese-based products. Setting up a manufacturing plant for Manganese(II) sulphate offers businesses an opportunity to cater to these emerging markets while contributing to the global shift towards cleaner, renewable energy solutions. This article outlines the key aspects of establishing a Manganese(II) sulphate manufacturing plant, including market demand, production process, and necessary infrastructure.
What is Manganese(II) Sulphate?
Manganese(II) sulphate is a chemical compound primarily used as a precursor for the production of manganese metal and as an important additive in the production of animal feed and fertilizers. The compound appears as a white or pink crystalline powder and is highly soluble in water. It is produced through various methods, including the reduction of manganese ore with sulphuric acid.
The most notable use of Manganese(II) sulphate is in the manufacture of cathodes for lithium-ion batteries, which are essential for electric vehicles and renewable energy storage systems. This usage has placed Manganese(II) sulphate at the heart of the emerging electric vehicle and clean energy industries, driving its demand globally.
Get a Free Sample Report with Table of Contents@ https://www.expertmarketresearch.com/prefeasibility-reports/manganese-ii-sulphate-manufacturing-plant-project-report/requestsample
Market Demand and Growth Drivers
The global demand for Manganese(II) sulphate is primarily driven by the increasing use of electric vehicles (EVs) and renewable energy storage systems. With the growing focus on reducing carbon emissions and adopting sustainable transportation methods, the automotive sector is transitioning towards electric vehicles, many of which rely heavily on lithium-ion batteries. These batteries require manganese, and thus, Manganese(II) sulphate is in high demand for cathode production.
Besides its role in battery manufacturing, Manganese(II) sulphate has several applications in industries such as agriculture and animal nutrition. In agriculture, it is used as a fertiliser to treat soils deficient in manganese, an essential nutrient for plant growth. The compound is also added to animal feed to promote healthy growth, particularly in livestock such as pigs and poultry.
As the global demand for electric vehicles continues to rise, the market for Manganese(II) sulphate is expected to experience steady growth in the coming years. Additionally, the increasing adoption of renewable energy storage technologies, such as grid-scale battery storage systems, is further expected to drive demand for this compound.
Setting Up a Manganese(II) Sulphate Manufacturing Plant
Establishing a manufacturing plant for Manganese(II) sulphate requires careful planning and investment in key aspects such as raw materials, production technology, infrastructure, and regulatory compliance. Below are the essential components involved in setting up a Manganese(II) sulphate manufacturing facility.
1. Raw Materials and Supply Chain
The production of Manganese(II) sulphate begins with the mining and processing of manganese ores, typically sourced from countries like South Africa, Australia, and China. Manganese ore, which contains manganese in various oxidation states, is subjected to chemical treatment to obtain Manganese(II) sulphate. This requires the use of sulfuric acid and other reagents to facilitate the extraction process.
Ensuring a consistent and reliable supply of high-quality manganese ore is crucial for the success of the manufacturing plant. Establishing strong relationships with ore suppliers and ensuring a stable supply chain will help maintain production efficiency and meet market demand.
2. Production Process
The production process for Manganese(II) sulphate involves several key steps, including leaching, purification, and crystallisation. The most common method used for the production of Manganese(II) sulphate is the sulphuric acid leaching process. The manganese ore is first treated with sulphuric acid to release manganese ions into solution. The resulting solution is then purified to remove impurities before the manganese ions are precipitated as Manganese(II) sulphate crystals.
Once the crystals are formed, they are dried and packaged for shipment to customers. The manufacturing process must be carefully monitored to ensure the final product meets the required specifications, including purity, particle size, and consistency.
3. Technology and Equipment
To ensure efficient and cost-effective production, investing in the right technology and equipment is essential. The leaching process, for example, requires specialized reactors and equipment to ensure proper mixing and control of temperature and pressure. Additionally, filtration and purification systems are necessary to remove impurities from the solution.
In the crystallisation stage, temperature and cooling processes must be carefully controlled to facilitate the formation of Manganese(II) sulphate crystals. Finally, drying equipment is required to remove excess moisture from the crystals before packaging.
Automation technologies can also play a significant role in streamlining the production process, reducing manual labour, and enhancing product consistency. Incorporating automation systems such as conveyor belts, automated filling stations, and quality control sensors can increase efficiency and reduce production costs.
4. Infrastructure and Location
The location of the manufacturing plant is a critical factor in ensuring smooth operations. Proximity to raw material sources, such as manganese ore deposits, is advantageous, as it can reduce transportation costs and ensure a steady supply of materials. Additionally, access to infrastructure such as water, electricity, and transportation networks is essential for the efficient running of the plant.
Choosing a location that is well-connected to key markets will also be important for distribution. If the plant is located near ports or railways, it can facilitate the export of Manganese(II) sulphate to international markets, where demand is growing.
5. Environmental Considerations
The production of Manganese(II) sulphate involves the use of hazardous chemicals such as sulphuric acid and the generation of waste by-products. To ensure that the plant operates in an environmentally responsible manner, it is essential to comply with local and international environmental regulations. Wastewater treatment facilities must be installed to handle the effluents produced during the leaching and purification processes.
Additionally, measures should be taken to minimize air pollution, especially if the plant is located in an area with high population density. Proper waste management systems should be put in place to safely dispose of any toxic or non-biodegradable materials.
Sustainability should be a priority throughout the plantβs operations, from sourcing raw materials responsibly to implementing energy-efficient production techniques. Companies that focus on sustainability and environmental responsibility will be better positioned to meet the growing consumer demand for environmentally friendly products.
6. Regulatory Compliance and Certification
Establishing a Manganese(II) sulphate manufacturing plant also requires compliance with various regulatory and safety standards. These regulations may vary depending on the country and region, but they generally cover health and safety, environmental impact, product quality, and manufacturing standards.
For example, companies involved in the production of chemicals must adhere to regulations set by bodies such as the Environmental Protection Agency (EPA) or the European Chemicals Agency (ECHA). Obtaining certifications such as ISO 9001 (quality management) or ISO 14001 (environmental management) can help build credibility and ensure that the plant operates efficiently and responsibly.
7. Market Entry and Distribution Strategy
To effectively penetrate the market, it is essential to have a clear distribution strategy. Manganese(II) sulphate is used in various industries, including battery manufacturing, agriculture, and animal nutrition. Therefore, identifying key market segments and targeting them with tailored marketing strategies is crucial.
Building partnerships with battery manufacturers, fertilizer companies, and animal feed producers can help secure long-term contracts and establish a stable customer base. In addition, creating an efficient supply chain that ensures timely delivery of products to customers is essential for maintaining a competitive edge in the market.
Given the growing demand for electric vehicles and renewable energy storage systems, international markets also present significant opportunities for expansion. Exporting Manganese(II) sulphate to countries that are investing heavily in clean energy infrastructure, such as those in Europe, North America, and Asia, can open up new revenue streams.
Challenges in Manganese(II) Sulphate Production
Despite the promising opportunities, there are several challenges that manufacturers may face when setting up a Manganese(II) sulphate production plant. These include fluctuations in raw material prices, regulatory hurdles, environmental concerns, and the need for continuous technological upgrades to remain competitive. Furthermore, managing waste and ensuring sustainable practices are crucial for long-term success.
However, by addressing these challenges effectively, businesses can tap into the growing market for Manganese(II) sulphate and play a vital role in the global shift toward sustainable energy solutions.
Leave a Reply