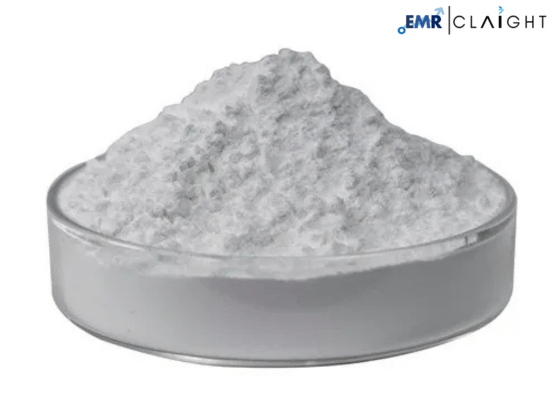
Magnesium fluoroborate is a significant compound widely used in industries like metallurgy, chemical synthesis, and pharmaceuticals. Known for its unique properties, it serves as a vital reagent in various applications, including catalysis and material production. Setting up a manufacturing plant for magnesium fluoroborate in 2025 requires an understanding of the production process, necessary equipment, and market potential. This article provides a detailed overview of the key aspects involved in establishing such a facility.
Understanding the Manufacturing Process
The production of magnesium fluoroborate involves multiple stages to ensure a high-purity and industrial-grade product. Below are the critical steps:
- Raw Material Preparation:
High-quality raw materials, including magnesium compounds and fluoroborate precursors, are sourced and prepared for processing. Purity at this stage is crucial for the end product. - Chemical Processing:
Magnesium fluoroborate is synthesised through a controlled chemical reaction involving magnesium salts and fluoroborate sources. This step requires precision to achieve the desired chemical composition. - Purification:
The crude product undergoes purification to remove any impurities, ensuring the final compound meets industrial standards. This step often involves crystallisation or filtration techniques. - Drying and Packaging:
The purified compound is dried to remove any residual moisture and then packed in airtight containers to preserve its quality during storage and transportation.
Get a Free Sample Report with Table of Contents@ https://www.expertmarketresearch.com/prefeasibility-reports/magnesium-fluoroborate-manufacturing-plant-project-report/requestsample
Essential Machinery for Manufacturing
Setting up a magnesium fluoroborate manufacturing plant requires investment in specialised machinery to ensure efficiency and quality. Key equipment includes:
- Reaction Vessels: For controlled chemical reactions.
- Filtration Systems: To remove impurities during the purification stage.
- Drying Units: To eliminate moisture and stabilise the product.
- Storage Tanks: For raw materials and final products.
- Packaging Equipment: For secure and contamination-free packaging.
Modern machinery with automation capabilities ensures consistency, reduces wastage, and enhances productivity in the manufacturing process.
Quality Control in Magnesium Fluoroborate Production
Quality control is essential to maintain the integrity and effectiveness of magnesium fluoroborate. Key aspects include:
- Raw Material Inspection: Ensuring the purity and suitability of all inputs.
- Process Monitoring: Regular checks during synthesis to maintain consistency.
- Purity Testing: Conducting laboratory tests to verify the chemical composition of the final product.
- Moisture Analysis: Ensuring the product meets required dryness levels for industrial use.
- Packaging Integrity: Ensuring airtight and secure packaging to prevent contamination.
Market Trends for Magnesium Fluoroborate in 2025
Magnesium fluoroborate has diverse industrial applications, driving its demand globally. Key trends influencing the market include:
- Metallurgical Applications: Increasing use in alloys and metal processing industries.
- Chemical Synthesis: Its role as a catalyst in various chemical reactions supports market growth.
- Pharmaceutical Demand: Use in pharmaceutical formulations as a specialised compound.
- Sustainability Practices: Growing demand for eco-friendly and high-purity reagents.
- Regional Growth: Expansion in emerging markets due to industrialisation.
Setting Up a Manufacturing Plant: Key Considerations
Establishing a magnesium fluoroborate manufacturing plant involves strategic planning and compliance with industry standards. Important considerations include:
- Location Selection:
Choose a site with easy access to raw materials, utilities, and transportation infrastructure. - Regulatory Compliance:
Adhere to environmental and safety regulations to ensure smooth operations. - Workforce Training:
Train staff to handle specialised equipment and maintain quality standards. - Cost Optimisation:
Implement cost-saving measures, such as efficient raw material usage and energy conservation. - Market Research:
Identify potential customers and tailor production volumes and quality accordingly.
Challenges in Magnesium Fluoroborate Manufacturing
Despite its market potential, magnesium fluoroborate manufacturing presents some challenges:
- Raw Material Costs: Fluctuations in the prices of magnesium compounds and fluoroborates can affect production costs.
- Regulatory Hurdles: Complying with stringent environmental and safety regulations can be complex.
- Quality Assurance: Maintaining consistent quality requires advanced testing and monitoring systems.
- Market Competition: The increasing number of manufacturers in this sector intensifies competition.
Leave a Reply