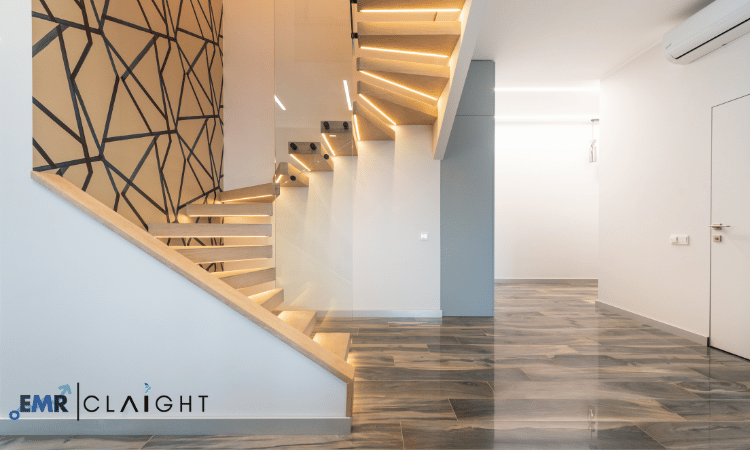
Fluted laminates have gained significant popularity in the interior design and construction sectors due to their durability, versatility, and aesthetic appeal. These high-performance materials are widely used in both residential and commercial applications, offering a unique combination of strength, visual appeal, and lightweight properties. The growing demand for modern, environmentally friendly materials in the construction and interior design industries has driven the establishment of fluted laminate manufacturing plants. This article explores the key elements involved in setting up a fluted laminate manufacturing plant, from sourcing raw materials to production processes and market opportunities.
Understanding Fluted Laminates
Fluted laminates are composite materials made from multiple layers of paper or plastic sheets, bonded together with a resin or adhesive. The result is a lightweight, durable, and flexible material with a corrugated or fluted structure. This structure gives fluted laminates their distinctive ribbed appearance, which provides both functional and decorative benefits. The fluted design enhances the strength-to-weight ratio of the laminate, making it ideal for use in applications where lightweight and strong materials are needed.
Fluted laminates are used in a variety of applications, including wall panels, partitions, furniture, and ceilings. These materials are particularly popular in commercial spaces such as offices, hotels, and retail outlets, where their modern look and durability are highly valued. Additionally, fluted laminates are also used in the production of decorative surfaces in residential homes, providing an affordable and aesthetically pleasing alternative to solid wood or other materials.
Get a Free Sample Report with Table of Contents@ https://www.expertmarketresearch.com/prefeasibility-reports/fluted-laminates-manufacturing-plant-project-report/requestsample
Market Demand and Opportunities
The market for fluted laminates has seen a steady increase, driven by rising consumer demand for innovative and stylish building materials. The demand for these materials is expected to continue growing, supported by the increasing focus on modern interior design trends and the desire for functional yet attractive surfaces.
Fluted laminates are particularly appealing because they offer a variety of aesthetic options. With a range of colours, textures, and finishes available, manufacturers can cater to a wide variety of design preferences. Furthermore, these laminates are an environmentally friendly alternative to traditional materials, such as solid wood, due to their lower environmental footprint and potential for recycling.
In addition to aesthetic advantages, the strength and durability of fluted laminates make them suitable for high-traffic areas, such as commercial buildings, public spaces, and healthcare facilities. The growing emphasis on sustainability and eco-friendly building materials further supports the demand for fluted laminates, as they are often made using renewable resources and can be recycled after use.
The market for fluted laminates is also supported by the rising demand for modular construction and interior solutions, where ease of installation and adaptability are important factors. As the construction industry increasingly moves toward more flexible and efficient building techniques, fluted laminates offer an ideal solution for creating stylish and functional spaces with minimal effort.
Raw Materials and Sourcing
The production of fluted laminates begins with the sourcing of raw materials. The primary raw materials used in the production of fluted laminates are paper, plastic, and resin. These materials are chosen for their durability, strength, and flexibility, which are essential qualities for producing high-quality laminates.
Paper-based fluted laminates are typically made from kraft paper, which is known for its strength and ability to withstand pressure and impact. The paper is coated with a resin to improve its resistance to moisture and environmental wear. In the case of plastic-based laminates, polypropylene or polyethylene is commonly used due to their superior strength and resistance to wear, moisture, and heat.
In addition to the basic materials, adhesives and coatings are required to bond the layers of paper or plastic together and create the desired fluted structure. The adhesive must be strong enough to hold the layers together under pressure, yet flexible enough to allow the laminate to maintain its shape and strength.
Sourcing high-quality raw materials is essential for ensuring that the final product meets industry standards and consumer expectations. Manufacturers must establish relationships with reliable suppliers to ensure the consistent availability of high-quality paper, plastic, and resin. The sustainability of the raw materials is also an important consideration, as consumers are becoming increasingly conscious of the environmental impact of the products they purchase.
Production Process
The production of fluted laminates involves several key stages, each of which plays a vital role in achieving the desired product quality and performance. The production process typically involves the following steps:
1. Preparation of Raw Materials
The first step in the manufacturing process is the preparation of the raw materials. For paper-based laminates, this involves cutting the kraft paper into sheets of the appropriate size. In the case of plastic-based laminates, the plastic sheets are cut to the desired dimensions. The sheets are then treated with a coating or resin to enhance their durability and moisture resistance.
2. Forming the Fluted Structure
Once the materials are prepared, the next step is to form the fluted structure. This is typically done using a fluting machine, which applies pressure to the material to create the distinctive ribbed design. The fluting process can vary depending on the type of laminate being produced, but it generally involves a process of heating and pressurising the material to create uniform, evenly spaced ridges.
The fluting process is crucial for creating the strength-to-weight ratio that makes fluted laminates so popular in construction and interior design. The fluted design increases the surface area and adds rigidity to the laminate, without increasing its weight. This ensures that the laminate remains lightweight, yet strong and durable.
3. Bonding the Layers
After the fluted structure is formed, the individual layers of paper or plastic are bonded together using a strong adhesive or resin. This bonding process ensures that the laminate retains its integrity and does not lose its shape over time. The adhesive must be carefully applied to ensure that the layers are securely attached, without any gaps or weak spots.
4. Curing and Drying
Once the layers are bonded, the laminate is cured and dried to ensure that the adhesive has fully set and the laminate is stable. This step is essential for ensuring that the laminate is durable and resistant to moisture, heat, and environmental wear. The curing process also helps to set the final texture and finish of the laminate.
5. Cutting and Finishing
Once the laminate has been fully cured, it is cut to the desired size and shape. The laminate can be cut into sheets, panels, or any other configuration required for the intended application. Additional finishing processes, such as embossing or laminating decorative surfaces, can be applied to enhance the appearance and texture of the final product.
6. Quality Control and Testing
Before the fluted laminates are ready for distribution, they undergo a series of quality control tests to ensure that they meet industry standards for strength, durability, and appearance. These tests may include tests for moisture resistance, impact strength, and surface finish. Quality control is essential for maintaining consistency and ensuring that the final product is suitable for use in construction and interior design applications.
Packaging and Distribution
Once the fluted laminates have passed quality control, they are packaged for distribution. Packaging plays a crucial role in protecting the laminates during transport and storage. The laminates are typically wrapped in protective plastic or cardboard to prevent damage and maintain their quality.
Distribution channels for fluted laminates can include wholesalers, construction companies, and interior designers. Manufacturers can also explore retail markets, offering their products directly to consumers through home improvement stores or online platforms.
Given the growing popularity of fluted laminates, manufacturers may also consider expanding their reach to international markets. The versatility and aesthetic appeal of these materials make them suitable for a wide range of global applications, from residential homes to commercial buildings.
Sustainability Considerations
Sustainability is a growing concern in the manufacturing industry, and fluted laminate production is no exception. Manufacturers can adopt several practices to reduce the environmental impact of their operations. This includes sourcing raw materials from sustainable suppliers, reducing waste through recycling initiatives, and using energy-efficient production techniques.
Fluted laminates themselves are often seen as a more sustainable alternative to traditional materials like wood or metal, as they use fewer raw materials and are often made from recyclable resources. Offering environmentally friendly options can be a key selling point for manufacturers looking to attract eco-conscious consumers and businesses.
Conclusion
The growing demand for innovative, aesthetically appealing, and sustainable materials makes fluted laminates an attractive option for the construction and interior design industries. Setting up a fluted laminate manufacturing plant offers significant potential for businesses to tap into a rapidly expanding market. By focusing on high-quality raw materials, efficient production processes, and a strong emphasis on sustainability, manufacturers can position themselves as leaders in this competitive and innovative market.
Leave a Reply