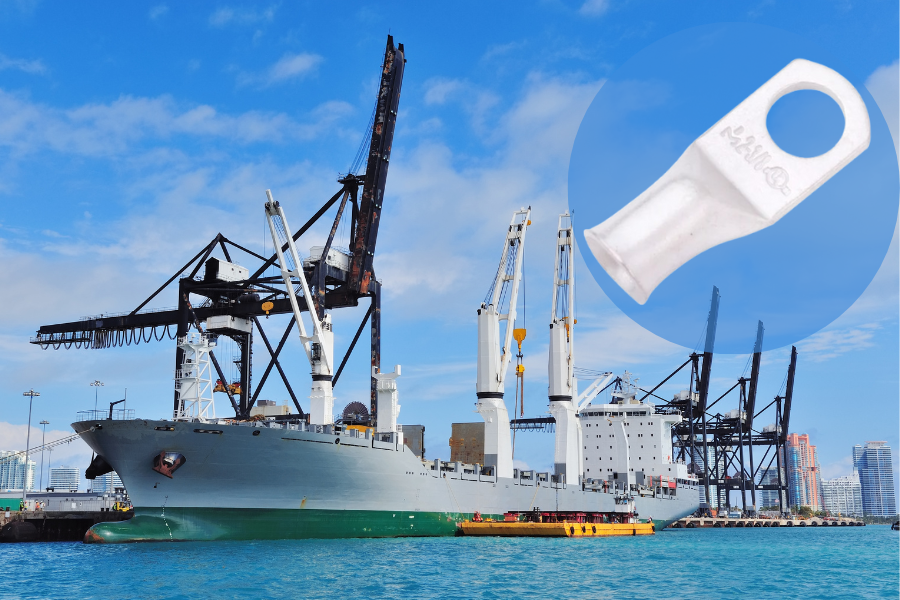
Marine electrical systems are critical to the operation of boats, yachts, and other water vessels. Battery cable lugs are an essential part of this system, ensuring reliable connections between cables and batteries. Proper installation and maintenance of these lugs are crucial for both safety and optimal performance. However, many boat owners and technicians make mistakes when handling marine battery cable lugs, leading to connection issues, equipment failures, or even safety hazards.
In this blog, we’ll explore the most common mistakes to avoid when using marine battery cable lugs to ensure the longevity and reliability of your electrical system.
1. Using Incorrectly Sized Cable Lugs
One of the most common mistakes is using cable lugs that are either too small or too large for the wires or cables they are meant to connect. Marine battery cables come in different gauges, and choosing the right lug size is essential for maintaining a solid and safe connection.
- Too Small Lugs: If the lug is too small, it may not properly fit the cable, leading to poor electrical contact. This can cause excessive heat buildup, increasing the risk of electrical failure or fire.
- Too Large Lugs: On the other hand, using a lug that is too large can result in a loose connection, creating resistance and possibly causing corrosion at the joint.
Always choose cable lugs that match the wire’s size (gauge) and the amperage requirements of the system. If in doubt, consult the manufacturerβs recommendations or seek professional advice.
2. Neglecting to Properly Strip the Cable
Stripping the insulation from the cable is a delicate process, and improper stripping can lead to several issues. Too little wire exposure can result in a weak connection, while stripping too much can expose the wire to corrosion and damage.
- Not Enough Wire Exposure: If you donβt strip enough of the cable, the lug wonβt have sufficient contact with the wire. This can create a poor connection, leading to voltage drops, power loss, and heating issues.
- Stripping Too Much: If you strip too much insulation, the exposed wire may be prone to corrosion, especially in the harsh marine environment. Inadequate insulation can also cause accidental short circuits or grounding issues.
Use the appropriate wire stripper for the job, ensuring the cable is stripped to the right length (usually just enough to cover the connector area). This will help ensure a clean and secure connection.
3. Improper Crimping or Soldering Techniques
Crimping and soldering are two methods used to secure cable lugs to wires, and both need to be done correctly. Crimping tools must be calibrated for the right gauge, and the crimping process must be firm without damaging the wire.
- Crimping Mistakes: Crimping too lightly will result in a loose connection, while crimping too hard can damage the wire strands and reduce conductivity. A properly crimped lug should fit tightly on the wire, with no visible gaps between the wire and the lug.
- Soldering Mistakes: While soldering can offer a reliable connection, excessive solder can form a brittle joint that may fail under vibration or thermal changes, which are common in marine environments. It’s also easy to overheat the cable during soldering, causing damage to the wire.
If youβre crimping, use a high-quality, properly calibrated crimping tool. For soldering, ensure you apply the right amount of heat and solder to avoid creating a weak connection.
4. Not Using the Right Materials for Marine Conditions
Marine environments are particularly harsh, with high humidity, saltwater exposure, and temperature fluctuations. Using cable lugs made from materials that are not designed to resist corrosion can quickly lead to degradation and failure.
- Corrosion: Copper lugs are common, but they can corrode quickly when exposed to saltwater unless they are coated with anti-corrosive material such as tinned copper or brass. Non-tinned copper lugs may tarnish or corrode, compromising the connection and the safety of the electrical system.
- Choosing Poor Materials: Stainless steel lugs are another option, known for their resistance to corrosion, but they are often more expensive. However, itβs essential to balance cost and durability for long-term performance.
Always opt for tinned copper or other corrosion-resistant materials specifically designed for marine applications to ensure the longevity and effectiveness of your electrical system.
5. Ignoring the Importance of Tightening the Lug Connections
Once the lug is crimped or soldered onto the cable, itβs crucial to tighten the bolt or terminal that secures the lug to the battery or electrical component. Over-tightening or under-tightening can both lead to problems.
- Over-tightening: This can cause the lug to deform or damage the cable, leading to poor contact or even breaking the wire.
- Under-tightening: Loose connections can cause intermittent contact, creating resistance, generating heat, and increasing the risk of fire or electrical malfunction.
Make sure to use a torque wrench and follow manufacturer guidelines to achieve the correct level of tightness.
6. Failing to Use Proper Insulation and Protection
Marine electrical systems are subjected to a range of environmental factors that can cause wear and tear on exposed wires and lugs. Failing to adequately insulate or protect cable lugs can result in short circuits, electrical shock, and corrosion.
- Exposed Lugs: Cable lugs that are not insulated or sealed can be exposed to water and corrosion. Over time, saltwater and moisture can cause the lugs to corrode, affecting the performance and safety of the electrical system.
- Lack of Protection: Ensure that all connections are adequately covered with protective boots or heat shrink tubing. This will keep moisture out and prevent corrosion, especially in critical areas like the battery terminals.
7. Not Inspecting and Maintaining the Connections Regularly
Even after youβve installed the marine grade heavy-duty lugs correctly, itβs important to inspect and maintain the connections regularly. Marine environments are particularly rough on electrical systems, and connections can loosen over time or suffer from corrosion.
Periodically inspect the battery cables, lugs, and terminals for signs of wear, corrosion, or damage. If any issues are found, replace the faulty lugs or cables immediately to prevent further complications.
Conclusion
Installing marine grade heavy-duty lugs may seem straightforward, but it requires attention to detail and an understanding of the unique challenges of the marine environment. By avoiding the common mistakes outlined above, you can ensure a more reliable, durable, and safe electrical connection for your vessel. Whether you’re replacing old connections or building a new system, always prioritize proper sizing, material selection, installation techniques, and regular maintenance for the best performance and safety.
Β
Leave a Reply