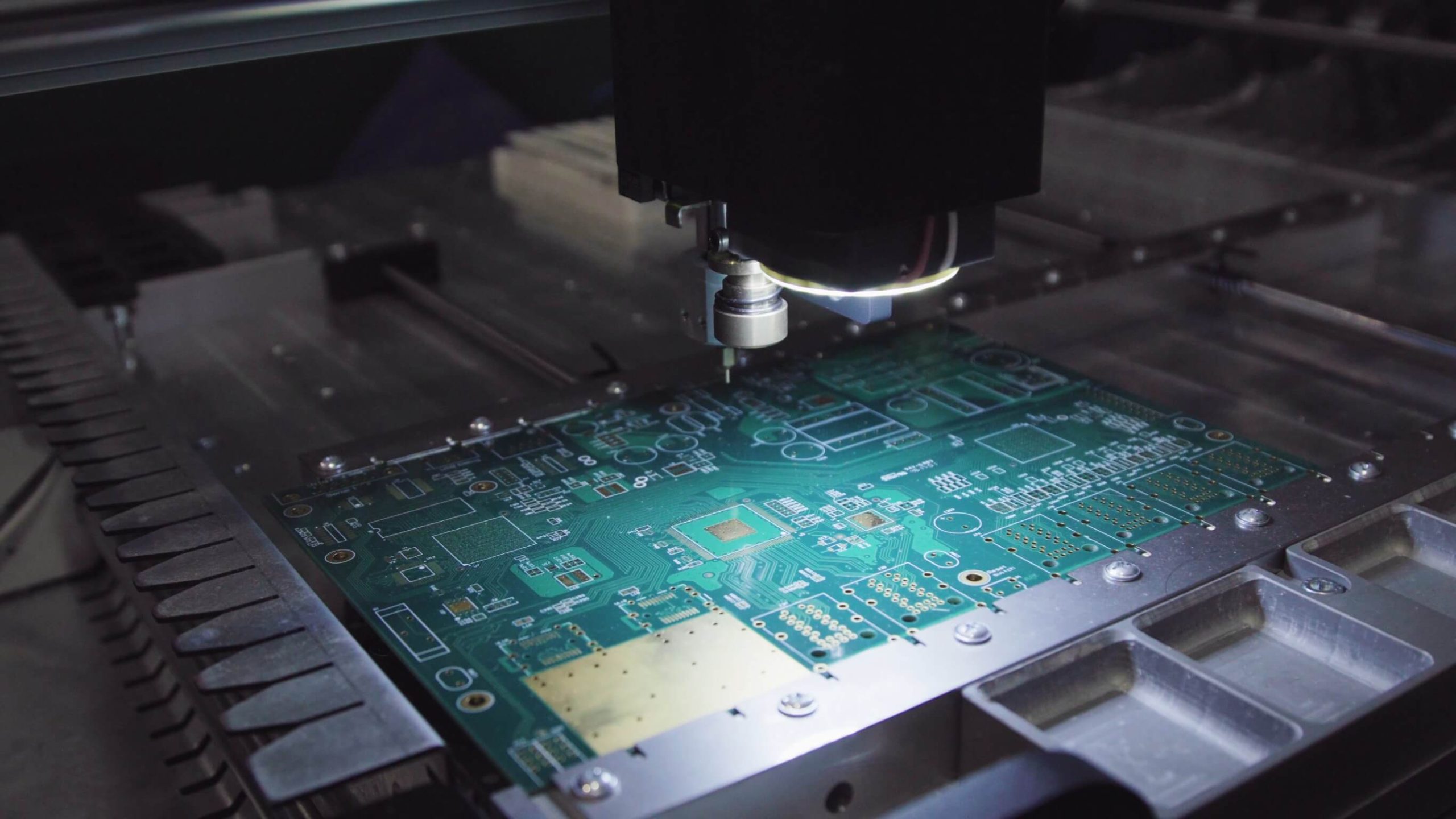
Printed circuit boards or PCBs are essential to nearly every modern electronic device, and while traditional PCBs work well in many applications, some industries require something more robust. Thatโs where metal core PCBs (MCPCBs) come in. But what exactly is a metal core PCB, and why are they considered a game-changer in high-performance electronics?
What is a Metal Core PCB?
As the name suggests, it contains a layer of metal (most commonly aluminum or copper) at its core. Unlike traditional PCBs that use fiberglass (FR4) as the substrate, metal core PCBs incorporate this metal layer to improve heat dissipation and durability.
These boards are often used in situations where traditional PCBs would struggle to maintain performance, such as in high-power LED lighting, automotive electronics, and industrial machinery. The ability to manage heat and withstand tough environmental conditions makes them indispensable in fields that demand reliability and efficiency.
Now that we know what they are, let’s look at the five traits that make metal core PCBs essential in certain applications.
5 Traits of a Metal Core PCB
- Superior Heat Dissipation
One of the amazing features of metal core PCBs is their high heat dissipation capabilities. Here’s why this matters: Excess heat can damage sensitive electronic components, reduce their lifespan, and, in some cases, even lead to device failure.
The metal core helps transfer heat away from heat-generating components (like LEDs or power transistors) to a heat sink or the surrounding environment, keeping the board and components cooler. This feature is especially crucial in applications like LED lighting, where components generate significant amounts of heat during prolonged use.
For example, in LED streetlights, the consistent dissipation of heat ensures longer-lasting lights and better energy efficiency – both critical for reducing maintenance costs and energy use.
- Enhanced Durability
MCPCBs are built to endure. Their construction with a metal core lends them not only thermal advantages but also higher structural strength compared to FR4 boards. The metal base layer acts as a support, making the board less prone to cracking under mechanical pressure or environmental stress.
This strength makes them suitable for vibration-heavy applications like automotive electronics, where constant motion and environmental wear are common. Imagine the PCB in the control unit of an electric car – constant vibrations, extreme temperatures, and the need for absolute reliability mean they need to be as robust as possible. Metal core PCBs excel in such environments.
- Improved Thermal Expansion Compatibility
When components heat up, they expand – a phenomenon known as thermal expansion. Mismatched thermal expansion between components and the substrate material can lead to stress and eventual cracking.
Metal core PCBs are designed to have better thermal expansion properties, as metals like aluminum and copper have thermal expansion coefficients closer to those of most electronic components. This compatibility minimizes damage and ensures longer-lasting electronic assemblies.
Take high-power devices like motor controllers or amplifiers. These systems generate tremendous amounts of heat and require PCBs that can handle the temperature swings without degrading performance. A metal core PCB is, quite literally, built for the job.
- Greater Versatility in Design
Another underrated trait of metal core PCBs is versatility. Depending on the application, MCPCBs can be tailored to meet specific needs. For starters, manufacturers can choose from various metal cores – aluminum is popular for its balance of cost and performance, while copper offers superior conductivity.
Further, manufacturers can selectively place the metal core in multilayer PCB designs to achieve thermal management where itโs needed most. This flexibility allows for custom solutions in complex devices where both electrical performance and thermal regulation are critical.
Ever considered how industrial machines maintain performance during rigorous operational cycles? That versatility in design often relies on well-engineered MCPCBs to deliver both the power and reliability needed for continuous use.
- Cost-Effective Over Time
Although metal core PCBs can initially cost more than traditional FR4 PCBs, they often prove to be the more cost-effective solution in the long term. Their durability means less frequent replacements, while their ability to efficiently dissipate heat reduces the likelihood of overheating and component failure.
For businesses looking to manufacture high-quality, reliable devices, these benefits often translate to significant cost savings down the line – especially in industries where downtime due to equipment failure can lead to major losses.
Picture this scenario: a smart LED lighting system in a corporate office. By choosing MCPCBs, maintenance teams worry less about replacing burnt-out components, and the organization saves on operational costs. This cost-effectiveness adds real value to the business.
Conclusion
Metal core PCB isnโt just a niche option โ they are becoming a necessity in many advanced electronic applications. Their ability to manage heat, endure mechanical and thermal stress, and provide a customizable design makes them stand out.
If you are designing electronics that demand longevity, high performance, and reliability, itโs time to explore whether MCPCBs are right for your next project.
Leave a Reply