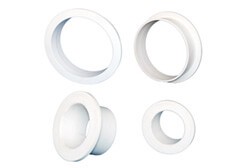
Glass nozzles play a crucial role in various industries, including chemical, pharmaceutical, and manufacturing. They are known for their durability, resistance to corrosion, and ability to handle high temperatures. Understanding the glass nozzles manufacturing process can help in selecting the right product for specific applications, such as in a Glass Lined Reactor Nozzle. This guide provides a detailed, step-by-step overview of how glass nozzles are made.
What Are Glass Nozzles?
Glass nozzles are components made from high-quality glass materials designed to control the flow of liquids or gases. They are widely used in industrial equipment where precision, chemical resistance, and high-temperature tolerance are needed. Glass nozzles come in different shapes and sizes to suit a variety of applications, including spray systems, laboratory apparatus, and chemical reactors.
Key Materials Used in Glass Nozzle Manufacturing
The primary material used in manufacturing glass nozzles is borosilicate glass. Borosilicate glass is preferred due to its high thermal resistance, durability, and chemical stability. Other specialized glass types may also be used, depending on the application requirements. Additionally, metal components or coatings might be added to enhance the nozzle’s functionality and durability.
Step-by-Step Manufacturing Process of Glass Nozzles
1. Design and Specification
The first step in the manufacturing process involves designing the glass nozzle based on the specific requirements of its intended use. This includes determining the size, shape, flow capacity, and any special features such as spray patterns or threaded connections. Engineers and designers work closely to create detailed drawings and 3D models of the nozzle.
2. Material Selection
Once the design is finalized, the appropriate type of glass is selected. As mentioned earlier, borosilicate glass is often chosen for its exceptional properties. The quality of the glass material is critical to ensure the final product meets industry standards and performs reliably in challenging conditions.
3. Glass Shaping
The shaping process involves heating the glass material until it reaches a malleable state. This is typically done in a glass furnace where temperatures can exceed 1,000 degrees Celsius. Skilled technicians use tools to shape the softened glass into the desired nozzle form, whether it involves blowing, molding, or stretching techniques.
4. Forming the Nozzle
During this stage, specific features of the nozzle, such as the tip, threads, or connections, are created. Depending on the design, this might involve additional molding or precision cutting. For nozzles used in Glass Lined Reactor Nozzles, precision is key to ensure a proper fit and optimal performance in chemical processing applications.
5. Annealing
After shaping, the glass nozzles undergo an annealing process. This involves gradually cooling the glass to relieve internal stresses and enhance its strength. The glass is placed in an annealing oven, where the temperature is slowly reduced over several hours. This step is crucial to prevent cracking or breaking under high-stress conditions.
6. Coating and Finishing
Depending on the application, some glass nozzles require additional coatings to enhance their performance. For example, a special coating might improve chemical resistance or reduce friction. The nozzles are also polished to ensure a smooth finish and checked for any imperfections that might affect performance.
7. Quality Control
Quality control is a vital part of the manufacturing process. Each glass nozzle undergoes rigorous testing to ensure it meets the required standards. This includes checking dimensions, durability, chemical resistance, and overall performance. Any nozzles that do not meet the standards are discarded or reworked.
8. Packaging and Distribution
Finally, the finished glass nozzles are carefully packaged to avoid damage during transportation. Packaging typically involves protective materials and labeling to indicate the specifications of the product. The nozzles are then distributed to clients or stored for future orders.
Applications of Glass Nozzles
Glass nozzles are widely used in various industries. In the chemical industry, they are used in Glass Lined Reactor Nozzles to manage the flow of chemicals safely and efficiently. They are also utilized in laboratory settings for precision tasks and in manufacturing environments where chemical resistance and temperature stability are required.
Conclusion
The glass nozzles manufacturing process involves several critical steps, from design and material selection to forming, annealing, and quality control. By understanding this process, industries can make informed decisions when selecting glass nozzles for their specific needs. Whether for use in a Glass Lined Reactor Nozzle or other industrial applications, high-quality glass nozzles offer durability, safety, and performance benefits.
Leave a Reply