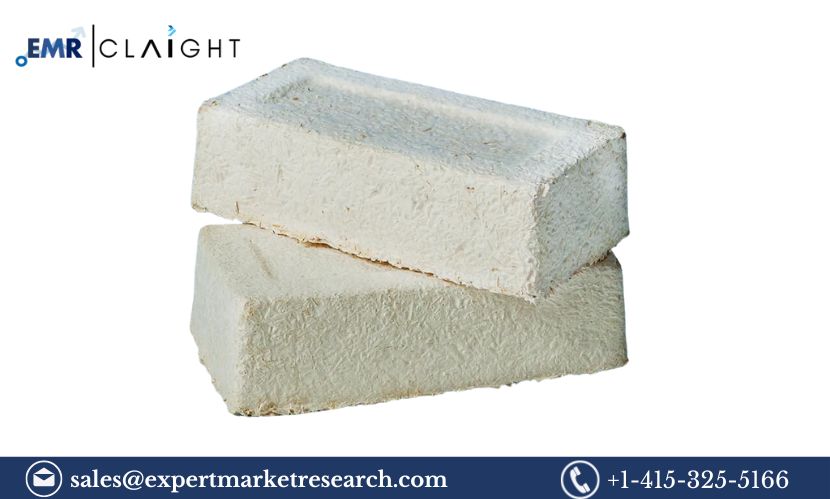
Introduction
The construction industry is evolving, with a growing focus on sustainability and eco-friendly alternatives. One such innovation is the use of mycelium bricks, a sustainable building material made from the root structure of fungi. The Mycelium Brick Manufacturing Plant Project Report delves into the feasibility, design, and technical aspects of setting up a plant dedicated to producing mycelium bricks. These bricks are gaining attention for their strength, lightweight properties, and environmental benefits, including their ability to reduce carbon footprints in construction. In this article, we will examine the processes involved in the production of mycelium bricks, the market potential, plant design, and financial considerations required for setting up a successful manufacturing facility.
What Are Mycelium Bricks?
Mycelium bricks are made by cultivating the mycelium of fungi, which is the vegetative part of the organism, and using it as a binding agent for organic materials like agricultural waste, sawdust, and hemp. The mycelium grows into the organic material, binding it together and forming a solid structure that is both lightweight and durable. Once the mycelium has fully colonized the material, the brick is dried and cured to ensure its stability and strength.
Mycelium bricks offer several advantages over traditional building materials. These include their biodegradability, thermal insulation properties, and the fact that they can be produced using agricultural by-products, making them a highly sustainable alternative. Mycelium is also renewable, as it can be grown quickly and harvested without the need for extensive land or water resources, unlike traditional brick manufacturing processes that require substantial energy inputs and raw materials.
Market Demand and Applications of Mycelium Bricks
The demand for sustainable and green building materials is growing rapidly, as both governments and private entities are increasingly committed to reducing environmental impact. Mycelium bricks, with their eco-friendly credentials, fit perfectly into this trend. They can be used in a wide range of applications, from residential and commercial buildings to insulation in construction.
Key Applications:
- Construction: Mycelium bricks can be used as a sustainable alternative to traditional bricks for building walls and facades. Their insulating properties also help reduce energy consumption.
- Packaging: Mycelium-based products are already being used as packaging materials in place of plastics, providing an eco-friendly solution to the global plastic waste problem.
- Furniture: The lightweight and flexible nature of mycelium makes it suitable for use in the furniture industry, as it can be molded into different shapes and designs.
- Agricultural Industry: Mycelium can be used in creating eco-friendly, biodegradable pots and packaging for plants.
The increasing need for green and renewable materials in the construction sector, along with rising awareness of sustainability, makes the mycelium brick manufacturing plant a viable and profitable investment.
Get a Free Sample Report with Table of Contents@
Technical Process of Mycelium Brick Production
The process of manufacturing mycelium bricks involves several key steps that must be carefully controlled to ensure the quality of the final product. Here’s a breakdown of the main stages:
1. Selection of Raw Materials:
The first step in the production of mycelium bricks is selecting the right organic materials. These typically include agricultural by-products such as straw, sawdust, hemp, or other biodegradable organic waste. These materials serve as the substrate, or growing medium, for the mycelium. The quality and type of the substrate can affect the final strength and durability of the bricks.
2. Inoculation with Mycelium:
Once the substrate is prepared, it is mixed with fungal spores. The mycelium spores are added to the substrate in a controlled environment. The mixture is kept in optimal conditions of humidity, temperature, and airflow, which allow the mycelium to grow and colonize the organic material. This process typically takes a few weeks.
3. Growth and Colonization:
During this stage, the mycelium grows into the substrate, binding it together into a cohesive structure. The growing mycelium forms a network of threads (hyphae) that bind the organic material, creating a dense and solid structure. The growth period is carefully controlled to ensure that the mycelium fully colonizes the substrate.
4. Molding and Shaping:
Once the mycelium has fully colonized the substrate, the mixture is placed into molds to form bricks of the desired size and shape. The molds are designed to create uniform bricks that can be used in construction or other applications. The shaping process ensures that each brick has the correct dimensions and strength for its intended purpose.
5. Drying and Curing:
After molding, the mycelium bricks are dried to remove moisture content. This is a critical step to ensure that the bricks retain their strength and durability. In some cases, the bricks may also be subjected to a curing process that hardens the structure further, improving the final product’s overall stability and lifespan.
6. Quality Control and Testing:
Finally, the mycelium bricks are subjected to rigorous quality control measures. They are tested for strength, durability, and insulation properties to ensure they meet industry standards. The testing process is essential to ensure that the bricks are fit for use in construction and other applications.
Plant Design and Layout
Designing the layout for a Mycelium Brick Manufacturing Plant requires a thorough understanding of the production process, efficient space management, and adherence to safety standards. A well-designed plant can significantly improve productivity and reduce operational costs.
Key Aspects of Plant Design:
-
Space Allocation: A typical mycelium brick manufacturing plant requires space for the growing and curing process, equipment storage, raw material storage, and finished product inventory. The layout should be optimized to ensure smooth flow from one stage of production to the next.
-
Environmental Controls: The plant should have controlled environments for the mycelium growth phase. This includes temperature and humidity control systems to maintain ideal growing conditions for the mycelium. The factory should also include air filtration systems to ensure the space remains free from contamination.
-
Automation and Process Control: Automation can help improve efficiency and reduce human error. Automated systems can be implemented in mixing, inoculating, molding, and drying processes. A central control system can help monitor and adjust the process parameters in real-time, ensuring consistent product quality.
-
Energy Efficiency: Energy efficiency is an important consideration, as the production of mycelium bricks can be an energy-intensive process. Incorporating energy-saving technologies, such as heat recovery systems and efficient lighting, can help reduce operational costs and improve the sustainability of the plant.
-
Safety and Compliance: Safety is a critical aspect of plant design. Proper ventilation, fire safety systems, and employee safety protocols must be implemented to minimize risks. In addition, the plant must comply with local environmental regulations regarding waste disposal, emissions, and water usage.
Raw Materials and Supply Chain Considerations
A successful mycelium brick manufacturing plant relies on a steady supply of raw materials. These include organic substrates such as straw, sawdust, hemp, and other biodegradable waste. Securing reliable and cost-effective suppliers for these materials is essential to maintaining production schedules and controlling costs.
Supply Chain Management:
-
Raw Material Procurement: The plant needs to establish relationships with suppliers of organic substrates. These materials must be consistently available at competitive prices to avoid delays in production. In many cases, local sourcing of agricultural waste or by-products can help reduce transportation costs and carbon footprint.
-
Material Storage: Proper storage of raw materials is crucial to prevent contamination or degradation. The storage area should be dry and clean to maintain the quality of the organic materials before they are mixed with mycelium spores.
-
Distribution and Logistics: Once the mycelium bricks are produced, they need to be distributed to customers. This requires a reliable logistics network that can handle the transportation of large quantities of bricks to construction sites or other end-users.
Financial Considerations and Projected ROI
The investment required to set up a Mycelium Brick Manufacturing Plant involves several key cost components. These include the cost of land, building infrastructure, purchasing equipment, and obtaining raw materials. Financial projections are vital to determine the feasibility and profitability of the plant.
Cost Breakdown:
-
Capital Investment: This includes the cost of purchasing land, constructing the plant, and installing the necessary equipment for growing, molding, and curing mycelium bricks. The initial capital investment may range from hundreds of thousands to millions of dollars, depending on the scale of the operation.
-
Operating Costs: The ongoing operating costs of the plant will include raw material procurement, energy costs, labor, maintenance, and transportation. These costs should be carefully managed to maintain profitability.
-
Revenue Generation: Revenue will primarily come from the sale of mycelium bricks to the construction, packaging, and other industries. The pricing of the bricks will depend on production costs and market demand, which can fluctuate depending on the level of adoption of sustainable building materials.
-
Return on Investment (ROI): Given the rising demand for sustainable and eco-friendly materials, the ROI for a mycelium brick manufacturing plant is expected to be favorable. With efficient operations and a strong marketing strategy, the plant can achieve significant returns over time.
Regulatory and Environmental Considerations
Setting up a mycelium brick manufacturing plant requires compliance with various regulatory standards and environmental regulations. These include waste disposal, emissions control, and ensuring the plantβs operations do not harm the surrounding ecosystem. The plant must also meet the necessary certifications for producing building materials to ensure that the bricks are safe for use in construction projects.
Media Contact
Company Name: Claight Corporation
Contact Person: Lewis Fernandas, Corporate Sales Specialist β U.S.A.
Email: sales@expertmarketresearch.com
Toll Free Number: +1β415β325β5166 | +44β702β402β5790
Address: 30 North Gould Street, Sheridan, WY 82801, USA
Website: www.expertmarketresearch.com
Aus Site: https://www.expertmarketresearch.com.au
Leave a Reply