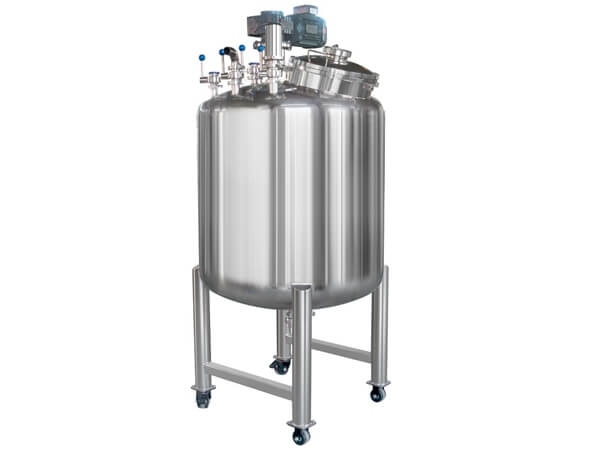
Mixing tanks play a crucial role in various industries, from food and beverage production to pharmaceuticals and chemical manufacturing. The efficiency of a mixing tank is largely determined by its flow patterns, which directly impact blending, reaction rates, and overall product consistency. Understanding how flow patterns affect performance can help industries optimize their processes, reduce production time, and enhance product quality.
In this article, we will explore different mixing tank flow patterns, their impact on performance, and how to optimize them for specific applications.
Understanding Mixing Tank Flow Patterns
Flow patterns in a mixing tank are dictated by tank geometry, impeller type, baffles, fluid properties, and operating conditions. There are three primary types of flow patterns:
1. Radial Flow
Radial flow occurs when the liquid moves outward from the center of the impeller toward the tank walls and then back toward the center. This pattern is common in flat-blade turbines and Rushton turbines.
- Advantages: Radial flow generates strong turbulence, which is useful for gas dispersion and solid suspension.
- Disadvantages: It may create dead zones in the tank where mixing is inefficient, leading to inconsistent blending.
2. Axial Flow
Axial flow is characterized by liquid moving parallel to the impeller shaft, creating an upward or downward motion. This pattern is common in propeller mixers and pitched-blade turbines.
- Advantages: Axial flow enhances circulation and homogeneity, making it ideal for applications requiring uniform mixing.
- Disadvantages: It may be less effective in breaking down solids compared to radial flow.
3. Tangential Flow
Tangential flow occurs when the fluid moves in a circular motion around the tank without significant vertical or radial movement. This flow is typically observed in unbaffled tanks or when using a vortex mixer.
- Advantages: It reduces shear forces, making it ideal for delicate suspensions and shear-sensitive products.
- Disadvantages: Poor axial and radial mixing can lead to longer mixing times and inefficient blending.
How Flow Patterns Affect Mixing Performance
1. Blending Efficiency
Efficient mixing tank ensure that all components are evenly distributed within the mixture. Axial flow is generally the best for blending applications because it promotes complete circulation and prevents stagnation.
2. Heat Transfer
In industries where temperature control is crucial, such as chemical processing and food production, the flow pattern influences heat distribution. Radial and axial flow patterns enhance heat transfer, ensuring uniform temperature across the tank.
3. Suspension of Solids
In pharmaceutical and chemical industries, solid particles must be evenly suspended in liquid mixtures. Radial flow is preferred for heavy solids, while axial flow works well for lighter suspensions.
4. Gas Dispersion
Gas-liquid reactions require efficient gas dispersion to maximize reaction rates. Radial flow patterns are more effective for gas dispersion as they create higher turbulence, helping break down gas bubbles.
5. Reduction of Dead Zones
Dead zones are areas where mixing is ineffective, leading to inconsistent product quality. Proper use of baffles and impeller positioning helps eliminate dead zones and improve overall performance.
Optimizing Mixing Tank Flow Patterns
To achieve optimal mixing performance, itβs essential to choose the right tank design, impeller type, and operational settings. Here are some tips for optimization:
1. Selecting the Right Impeller
- Pitched-blade turbines: Ideal for axial flow and general-purpose mixing.
- Flat-blade turbines: Suitable for radial flow and gas dispersion.
- Propellers: Best for low-viscosity liquids requiring strong axial flow.
2. Using Baffles to Prevent Vortex Formation
Baffles help disrupt circular flow patterns, preventing vortex formation and improving radial and axial mixing. Adding four baffles at 90-degree intervals in a cylindrical tank significantly improves mixing efficiency.
3. Adjusting Agitation Speed
The speed of the impeller affects the intensity of mixing. Higher speeds increase turbulence but may cause shear stress on sensitive products. Finding the right balance is key to efficient mixing.
4. Considering Tank Shape and Size
The shape and size of the mixing tank influence the flow pattern. Tall, narrow tanks promote axial flow, while short, wide tanks encourage radial flow. Choosing the appropriate dimensions ensures optimal performance.
5. Controlling Fluid Viscosity
Viscosity impacts how liquids flow within the tank. Low-viscosity fluids require higher speeds and axial flow, while high-viscosity fluids benefit from radial flow and slow agitation.
Conclusion
Understanding and optimizing mixing tank flow patterns is crucial for enhancing blending efficiency, heat transfer, and overall process performance. Selecting the right impeller, using baffles, adjusting speed, and considering tank geometry are key factors in achieving optimal mixing.
By carefully managing these aspects, industries can improve product consistency, reduce processing time, and enhance operational efficiency, leading to better quality and cost savings.
Leave a Reply