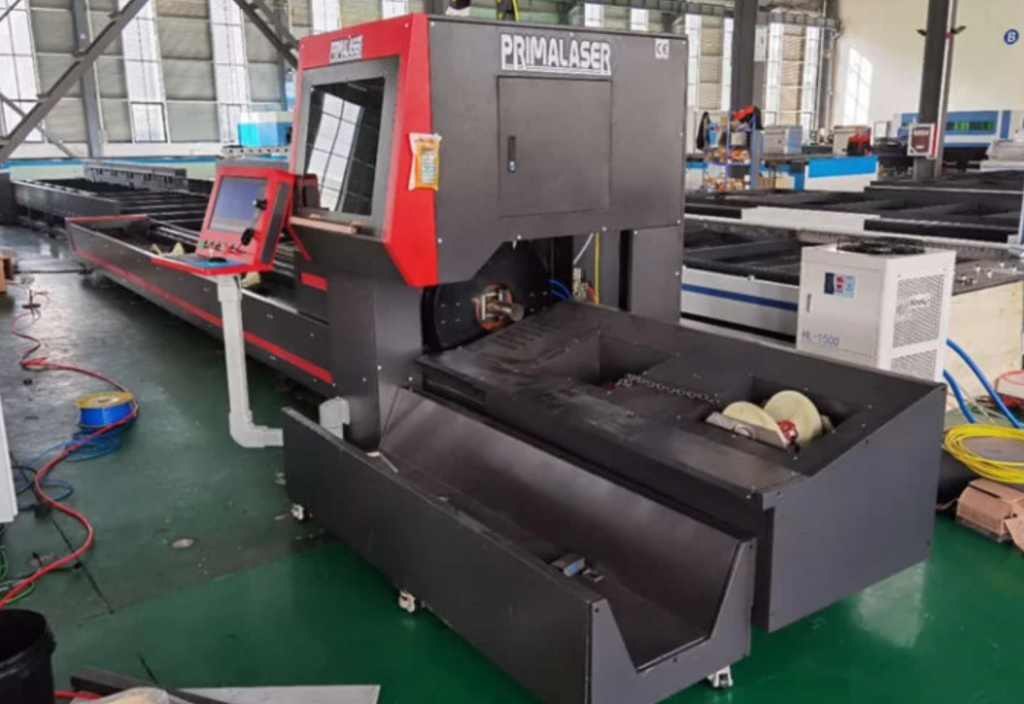
Laser machines are a crucial part of industries that require high-precision cutting, engraving, and marking. However, not all laser machine manufacturer produce machines with the same level of precision, even when working on identical materials. This variation often leads to confusion among buyers and raises questions about what influences these differences. To understand this, itβs essential to explore various factors that impact the precision of laser machines.
1. The Role of Laser Source Technology
The type of laser source plays a significant role in the performance of a laser machine. Some manufacturers use COβ lasers, while others opt for fiber lasers or diode lasers. Each laser type interacts with materials differently, affecting precision. For instance, fiber lasers are often preferred for metal cutting due to their ability to deliver high-intensity beams with minimal divergence. On the other hand, COβ lasers are commonly used for non-metal materials. The decision of a laser machine manufacturer to use a specific laser source depends on multiple factors, including cost, intended applications, and production efficiency.
2. Optical Components and Their Impact on Precision
Laser beams are directed and focused using optical components such as mirrors and lenses. The quality of these components varies between manufacturers, influencing the machineβs precision. Some manufacturers invest in high-quality optics that minimize beam distortion, ensuring consistent results. Others may use lower-grade components that lead to beam divergence, reducing accuracy. Even small deviations in optical alignment can result in noticeable inconsistencies in cutting and engraving outcomes.
3. Machine Frame and Structural Stability
The overall build quality of a laser machine is another critical factor that affects precision. A sturdy machine frame reduces vibrations and provides a stable platform for the laser head to move smoothly. Some laser machine manufacturers prioritize reinforced structures made from heavy-duty materials, ensuring minimal movement during operation. Others might use lighter frames, which can lead to slight shifts during high-speed cutting, ultimately affecting precision. The choice of materials and construction techniques reflects the manufacturer’s priorities, whether they focus on cost-effectiveness or long-term performance.
4. Motion Control and CNC System Variations
The motion control system in a laser machine determines how precisely the laser head moves along the X, Y, and Z axes. High-end laser machine manufacturers integrate advanced CNC (Computer Numerical Control) systems with precision stepper or servo motors. These components ensure the laser follows programmed paths with extreme accuracy. In contrast, machines with lower-grade motion control systems may experience minor deviations, leading to uneven cuts or inconsistent engraving depths. The selection of motion control technology varies between manufacturers based on their approach to balancing cost and precision.
5. Calibration and Software Algorithms
Precision in laser cutting and engraving is not only dependent on hardware but also on the software controlling the machine. Some laser machine manufacturers develop proprietary software with advanced calibration features that fine-tune laser intensity, speed, and focus dynamically. Others rely on generic software solutions with fewer optimization capabilities. The difference in software sophistication affects how well a machine adapts to material inconsistencies, ensuring consistent output across various production batches.
6. Cooling Systems and Their Effect on Laser Performance
Laser machines generate significant heat during operation, and effective cooling is essential to maintain consistent performance. Manufacturers use different cooling methods, such as air cooling or water cooling, to prevent overheating. Machines with efficient cooling systems maintain stable laser output, resulting in precise cuts. On the other hand, inadequate cooling can cause fluctuations in laser power, leading to variations in precision. The choice of cooling mechanism reflects a manufacturer’s approach to long-term machine reliability and performance.
7. Power Supply Stability and Its Influence on Accuracy
A stable power supply is crucial for maintaining consistent laser output. Some laser machine manufacturers integrate high-quality power units that ensure steady voltage and current delivery to the laser source. In contrast, lower-end machines may have fluctuations in power supply, leading to inconsistent cutting depths. The reliability of a machineβs electrical components directly affects its ability to produce precise results, especially in high-volume industrial applications.
8. Material Handling and Worktable Design
The way materials are positioned and secured on a laser machine also plays a role in precision. Some manufacturers design their machines with advanced worktables that feature automatic height adjustments and vacuum systems to hold materials firmly in place. Others use simpler designs that may not provide the same level of stability, resulting in slight misalignments during processing. This difference in design choices impacts how well a machine can maintain accuracy across repeated operations.
9. Maintenance Requirements and Long-Term Stability
Different laser machine manufacturers have varying approaches to machine maintenance and longevity. Some focus on producing machines with self-diagnostic systems that alert users about potential calibration issues before they affect precision. Others require manual adjustments and frequent recalibrations. Over time, the ease of maintenance and calibration determines whether a machine continues to deliver precise results or gradually loses accuracy due to wear and tear.
10. Research and Development Approach of Manufacturers
Every laser machine manufacturer follows a unique approach to research and development. Some companies continuously refine their designs based on industry feedback and technological advancements. They invest in innovations such as AI-assisted laser control, automatic material recognition, and smart adjustment features that enhance precision. Others may rely on older designs with minimal improvements, leading to noticeable variations in performance between different brands and models.
Conclusion
The variation in precision among laser machines from different manufacturers is a result of multiple interconnected factors. From the choice of laser source and optical components to the quality of CNC systems, cooling mechanisms, and software integration, each element plays a role in determining how accurately a machine performs. While some manufacturers prioritize high-end engineering and advanced technology to ensure top-tier precision, others focus on cost-effective solutions that may lead to slight inconsistencies in performance.
Understanding these factors can help buyers make informed decisions when selecting a laser machine that aligns with their specific needs. By evaluating the technological approaches of different laser machine manufacturers, businesses can ensure they invest in a machine that meets their accuracy and production requirements.
Leave a Reply