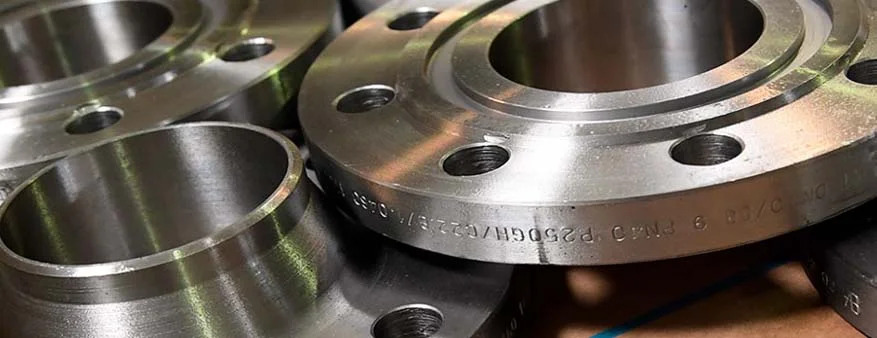
Alloy 600, also known as Inconel 600, is a nickel-chromium alloy widely recognized for its excellent corrosion and heat resistance. These properties make it a top choice for industries operating under harsh environments. Among its numerous applications, Alloy 600 flanges stand out as critical components in piping systems. They connect pipes, valves, pumps, and other equipment, ensuring a secure and leak-proof setup.
In this blog, weβll explore the unique properties of Alloy 600, the types of flanges made from this material, their advantages, and where they are commonly used.
What Is Alloy 600?
Alloy 600 is a versatile nickel-based alloy containing approximately 72% nickel, 14-17% chromium, and a small percentage of iron. This composition gives it remarkable mechanical strength and excellent resistance to oxidizing and reducing agents.
Key Properties:
- Corrosion Resistance: Withstand harsh chemicals, including acids, alkalis, and salts.
- Temperature Resistance: Performs well in high-temperature environments up to 2000Β°F (1093Β°C).
- Stress Corrosion Cracking: Resistant to stress-induced cracking in chloride-ion environments.
- Mechanical Strength: Retains structural integrity under pressure and temperature fluctuations.
These characteristics make Alloy 600 flanges suitable for demanding industrial conditions.
Types of Alloy 600 Flanges
Alloy 600 flanges come in various types to suit different applications. Below are the most common types:
-
Weld Neck Flanges
Weld neck flanges are known for their long tapered hub, which offers additional strength and resistance to stress. They are ideal for high-pressure and high-temperature applications. -
Slip-On Flanges
These flanges are easy to install and perfect for systems where stress on the flange is minimal. Slip-on flanges are cost-effective and versatile. -
Blind Flanges
Blind flanges are used to seal pipe ends, preventing flow. They are essential in systems that require regular inspection and maintenance. -
Socket Weld Flanges
These are commonly used in small-diameter, high-pressure piping systems. Socket weld flanges ensure a secure and leak-proof connection. -
Threaded Flanges
Threaded flanges are preferred for low-pressure applications and systems that require easy assembly and disassembly. -
Lap Joint Flanges
Often paired with a stub end, lap joint flanges allow for easy bolt alignment, making them suitable for systems requiring frequent disassembly.
Advantages of Alloy 600 Flanges
Using Alloy 600 flanges offers several benefits:
-
Corrosion Resistance
Alloy 600 flanges are highly resistant to corrosion, even in acidic and alkaline environments. This property makes them reliable in chemical processing and marine applications. -
Temperature Stability
The flanges maintain their strength and integrity in extreme temperatures, making them suitable for furnaces, heat exchangers, and power plants. -
Durability
With excellent mechanical strength, these flanges can withstand high pressure and resist wear and tear, ensuring long service life. -
Versatility
Their resistance to oxidizing and reducing environments allows them to be used in various industries, including petrochemical, aerospace, and nuclear power. -
Cost Efficiency
While the initial cost of Alloy 600 flanges may be higher, their durability and reduced maintenance requirements result in long-term savings.
Applications of Alloy 600 Flanges
Alloy 600 flanges find applications in industries where high performance and reliability are essential. Here are some examples:
1. Chemical Processing
- Used in reactors, heat exchangers, and piping systems that handle corrosive chemicals.
2. Power Generation
- Ideal for turbines, steam generators, and nuclear reactor components.
3. Aerospace Industry
- Utilized in jet engines and other components exposed to high temperatures and pressure.
4. Oil and Gas
- Employed in offshore platforms, refineries, and pipelines due to their resistance to seawater and corrosive substances.
5. Marine Engineering
- Perfect for shipbuilding and underwater applications because of their ability to resist chloride-induced corrosion.
6. Food Processing
- Used in systems that require high hygiene standards and resistance to acidic substances.
How to Select the Right Alloy 600 Flanges
Choosing the right flange type and specification is crucial for ensuring system efficiency. Consider the following factors:
-
Pressure and Temperature Ratings
Select flanges with appropriate ratings to match your operational requirements. -
Size and Dimensions
Ensure the flanges meet the size and dimensional standards (e.g., ANSI, ASME, DIN). -
Application Requirements
Choose the flange type (weld neck, slip-on, etc.) that suits your systemβs design and purpose. -
Surface Finish
Ensure the flangeβs surface finish meets the sealing requirements of your gasket material. -
Testing and Certification
Opt for flanges that come with proper testing and certification to guarantee quality and compliance.
Maintenance Tips for Alloy 600 Flanges
To extend the lifespan of Alloy 600 flanges, follow these maintenance tips:
-
Regular Inspection
Inspect the flanges for signs of wear, corrosion, or damage to prevent leaks and failures. -
Cleaning
Remove dirt, debris, and chemical residues regularly to maintain optimal performance. -
Proper Installation
Use the correct tools and techniques during installation to avoid unnecessary stress on the flanges. -
Lubrication
Lubricate the bolts and threads to ensure smooth assembly and disassembly. -
Follow Manufacturer Guidelines
Always adhere to the manufacturerβs recommendations for usage and maintenance.
Conclusion
Alloy 600 flanges are a reliable solution for industries that demand high performance in challenging environments. Their resistance to corrosion, heat, and mechanical stress makes them an indispensable component in various applications. By selecting the right type of flange and following proper maintenance practices, you can ensure the longevity and efficiency of your systems.
Whether you are in chemical processing, power generation, or marine engineering, Alloy 600 flanges offer the durability and reliability you need. Invest in high-quality Alloy 600 flanges today to enhance your operational efficiency and reduce downtime.
Leave a Reply